Our main industrial equipment incorporate sustainable and cost-effective solutions:
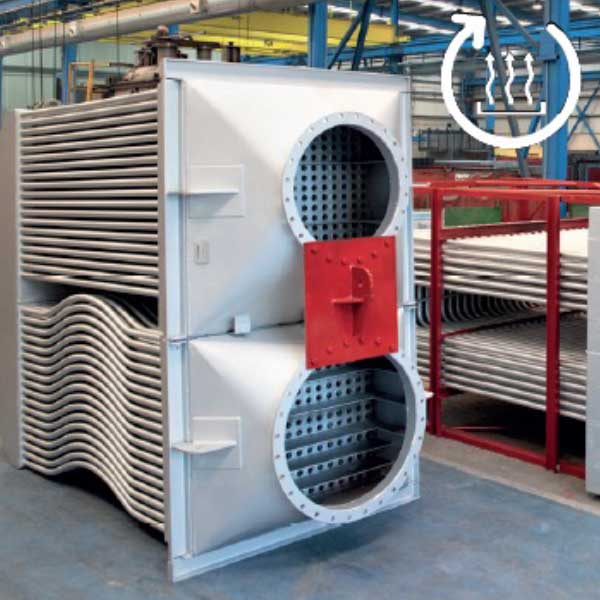
Energy recovery equipment
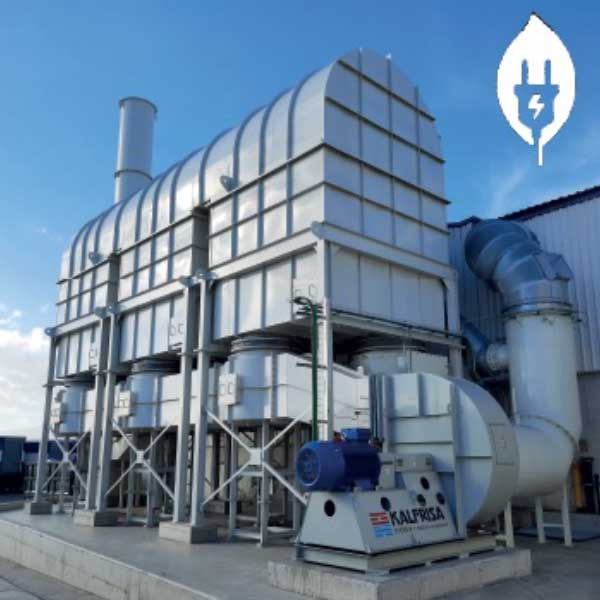
Dual electric equipment
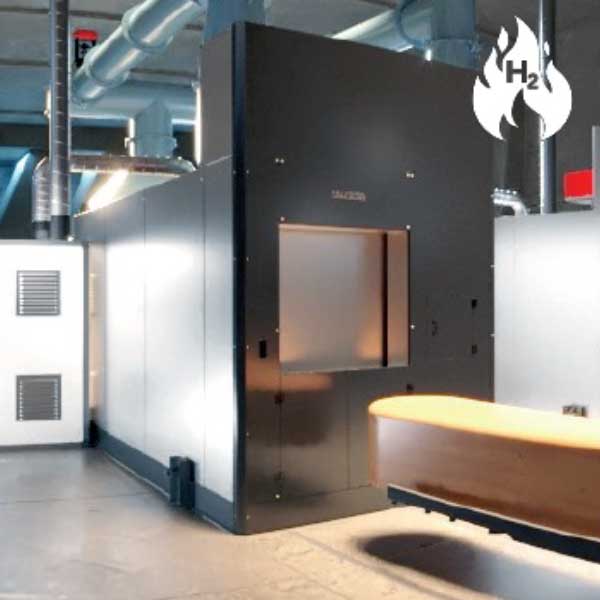
Hydrogen hybrid combustion equipment
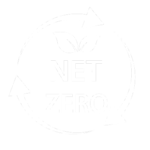
Our Technological Solutions:
KALFRISA’s Clean Technology Design and Validation Center is the result of our commitment to energy savings and to environment protection and it aims to drive progress towards industrial decarbonization.
These facilities allow us to help companies evaluate the implementation of clean technology solutions, such as:
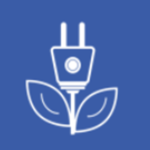
Process electrification
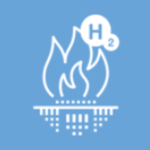
Clean combustion
OTHER SERVICES:
CONSULTANCY FOR DECARBONIZATION OF INDUSTRIAL THERMAL PROCESSES
Among our services, we highlight our consulting services for the hybridization to electricity or hydrogen of industrial thermal processes where combustion is usually involved.
KALFRISA offers support in the replacement of the fossil energy used in the current industrial thermal processes with alternatives of renewable origin.
Industries sensitive to these changes may include:
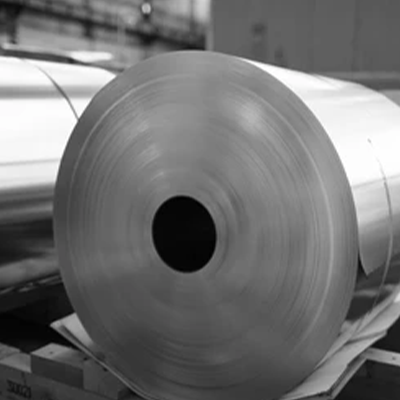
steel
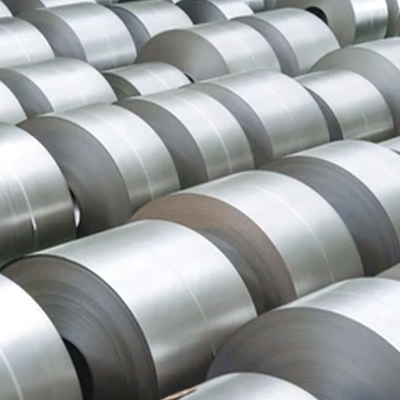
aluminum
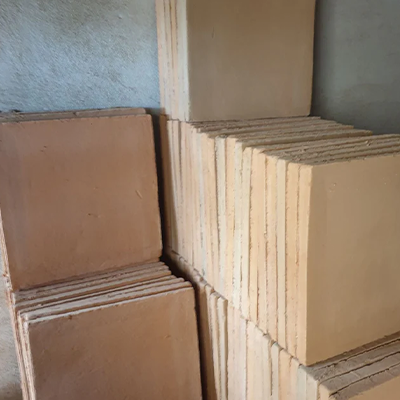
ceramic
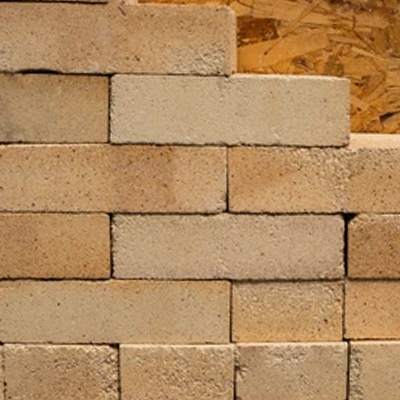
refractory
- impact of new kiln operating conditions on the processed material (steel, aluminum, ceramics, refractory, etc.);
- changes in the heat transfer mechanisms involved inside the furnace: convective and radiative;
- changes in the atmosphere inside the furnace and in contact with the process materials. In the case of H2 combustion, there is a reduction in CO2 and CO and an increase in water vapor and NOx emissions;
- changes in flame characteristics, both in shape and in temperature and radiation;
- changes in operating variables: air flow rates of fuels and resulting gases;
- impact on equipment downstream of the furnaces: e.g. energy recovery equipment;
- changes in the necessary instrumentation and safety measures.
We cover all stages from pre-audit to industrial implementation:
1
Pre-audit and evaluation of technical solutions
2
Semi-industrial phase tests for the evaluation of impacts on process materials under different conditions from 0 to 100% substitution, different powers up to 500 kWt and different temperature and pressure conditions.
3
Accompaniment to make the leap to industrial scale in plant:
- Studies of observed large-scale impacts
- Changes of industrial components (burners, valves, instrumentation…)
4
Support in the industrial implementation of new technologies